As the stepper motor is adjusted to take out the slack in the belt, it pulls the two rollers closer together which causes them to no longer be parallel with one another.
Using the Belt Sander example in which adjusting the belt sanders roller causes the sandpaper to skew left or right, the same principle applies here.
I fashioned a new end cap adjuster for the left side which split the adjustment plate into two pieces. John added some angle brackets for finer adjustment.
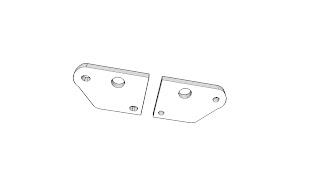
I drew it up in sketchup and cut it out, but did not actually end up using the holes I had provided along the bottom. I just used the existing bolts and tightened it down and it is holding just fine.
I tried measuring the distance between rollers on both ends to set them exactly the same distance apart on both ends, but I still ended up with skew present. I discovered that if the bit returns to the left of the origination hole, you just need to spread the left end of the rollers apart a bit more and that will move the material back to the right. It only takes a few thousandths, maybe .030 (1/32") to effect a big change, so I loosened the bolt very slightly and just tapped on the one roller to move it in very small increments.
I should also mention, that I had to enlarge the opening (for the hex shaft) on the far side of the left support panel (the one closest to the back of the machine) to give me some room to adjust the play.
I was able to totally eliminate the skew by doing this. Each time I would move it, I would run the bit back and forth along the X axis about 12 inches each way, repeating 4 times, and then would check to see where the bit returned.
Once I had the skew eliminated, I started doing runs using a test file made similar to my EO-Cub wing.
I made a 1", 2", 4", 8" and 10" test pattern and repeated it on the vertical and ran the tests which indicate backlash may be present. My cuts lengths were not exact, so I recalibrated manually moving the steps per unit 1 step at a time till I got the the lengths to come out exactly the same on both X and Y and both are now exactly 1,2,4,8 and 10" as per the SketchUP drawing.
I added some slots in the centers of these test parts and that helped to finally visually show the backlash. It can be seen as the bit entering the foam about 1/32" before where the slot ends up being cut.
Here is a picture of the test file I was cutting.
I probably need to try to take the stepper out and drill a dimple in the shaft where the set screw is touching the flat of the shaft. I suspect I am still getting a very tiny amount of backlash when the stepper reverses direction and hope by putting the dimple on the shaft that I can once and for all get the pulley to lock in place.
Of course that would mean I will have to go thru all of the adjustments again so I just tightened down the set screw some more without taking the stepper off.
I drew up a diagram to help me understand how the Backlash was affecting my cuts. It helped me visualize what the machine was doing and confirmed my theory.
In the test cut above, the slots along the top are supposed to line up with the slots along the bottom, but due to missed steps as the drive rollers change direction, I get about a 1/32" difference in alignment occuring in the parts I am trying to cut and build. This means I cannot fasten the ribs of my wing to the I-Beam without getting out an Xacto blade and opening up the slots on one side or the other so that they line up.
Update: 10 PM
I found this link which showed how to measure your backlash...
I measured my backlash by inputting G1 commands moving the X axis .1" at a time at a feed rate of 1 IPM with a dial indicator on the x axis. Putt, putt, putt, putt..... forward to .5" doing .1" at a time and then back to .4".
I was able to measure a .024 difference every time it reversed direction.
Very consistent.
I guess maybe tomorrow I will drag my wifes computer back out to the shop and play with Mach 3's backlash settings since the backlash code in the Planet-CNC is disabled.
The measured value corresponded very close to my guess of 1/32" (.031).
Sure explains why the EO-Cub Balsa cuts came out the way they did.
Now I can't help but wonder if the original pulleys with the finer teeth would produce less backlash.
Now I can't help but wonder if the original pulleys with the finer teeth would produce less backlash.
Guess, we'll find out when Mark gets the new drive rollers ready.
No comments:
Post a Comment